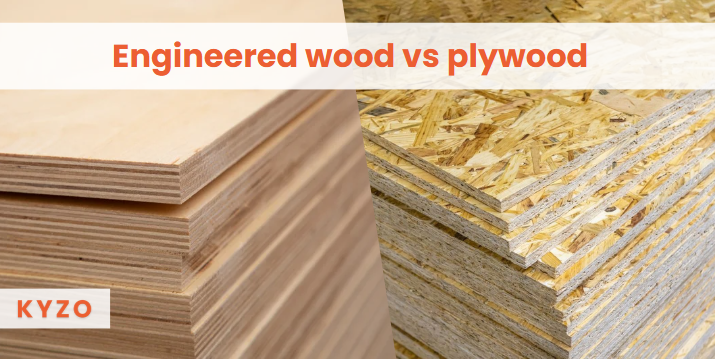
Engineered Wood vs Plywood: Key Factors to Consider for Optimal Material Selection in Woodworking
Share
Selecting the ideal wood for your woodworking project comes with both beauty appeal and stability practicality. Of course, in this situation, one of the most discussed issues is undoubtedly plywood and engineered wood. Each has its own superiority and both have their own set of properties, but a project often tends to become a real success only after familiarizing yourself with some of the less obvious but highly significant differences between them. Whether you're constructing furniture, cabinetry, flooring, or other wood-product elements, what you use can have a huge impact on the end result. This blog explores why you should consider the following when determining whether to use plywood or engineered wood so that you can make an educated choice based on your requirements.

Engineered Wood vs Plywood – A Guidebook
Engineered wood is the general term to use to describe wood products that are made by bonding wood particles, fibers, or veneers together with adhesives. Examples include MDF (Medium Density Fiberboard), HDF (High Density Fiberboard), and particle board. They are made to offer consistent and predictable behavior compared to natural wood, but with some special properties like water resistance or flame retardance. Plywood, however, is made of very thin layers of wood veneer bonded together with the direction of one layer at a right angle to the next layer. Plywood is solid and sturdy and has a broad range of applications in the manufacture of furniture, construction, and household repair.

The reason for this comparison is to discuss the main differences between engineered wood and plywood. You are able to determine which material best fits your project based on these differences if you are concerned with strength, expense, or the environment.
Major difference between engineered wood and plywood:
To simplify the decision-making process, let’s break down the comparison between engineered wood and plywood into key factors that matter most in woodworking projects. Below is a comparison table highlighting the critical parameters:
Factor | Engineered Wood | Plywood |
Composition | Made from wood fibers or particles | Made from thin layers of wood |
Moisture Resistance | Varies by product type (e.g., MDF is less resistant) | Generally more moisture resistant |
Bonding | Uses adhesives to bond fibers | Uses glue to bond wood layers |
Strength | Varies with product type | Generally stronger and more durable |
Durability | Moderate durability | High durability and stability |
Cost | Generally cheaper | More expensive, but highly durable |
Emissions | Can contain formaldehyde in adhesives | May emit formaldehyde based on grade |
Environmental Impact | Often made from recycled materials | Sourced from natural wood |
Raw Material, Water Resistance, Bonding
Raw material employed in engineered wood and plywood is very different. Wood particles or fibers with adhesives are employed to produce goods like particle board, HDF, and MDF. These may be engineered with specific characteristics, e.g., resistance to water or density for performance.
Conversely, plywood consists of natural wood veneers bonded together in layers. Plywood tends to be stronger in bonding strength, as the grain directions alternating provide structural strength. Plywood tends to be more water-resistant, particularly in marine-grade plywood, which is specifically designed for wet environments. Engineered wood products such as MDF are more prone to absorb moisture and swell or rot in more humid conditions. To give them their due, engineered wood products are treated to become more moisture-resistant.

When it is about strength and durability, plywood is more than its match. Because of its laminated make-up, plywood is less prone to warping and cracking, and therefore the most durable and appropriate for heavy use such as furniture, flooring, and building. Plywood wood veneer layers provide additional strength through stability.
Strength, Durability, Cost

Engineered wood products, depending upon what they are, will never be as structurally strong as plywood. Particle board and MDF, for instance, are usually more easily damaged by impact or water. However, they are still fine for indoor purposes and can be utilized in environments where heavy load is not of major concern.
Cost-wise, engineered wood products are usually cheaper than plywood. That is why they are widely used in projects where money is a problem. But if durability and strength are of the highest priority, the higher upfront cost of plywood might be worth the expense in the long term.
Applications, Emissions, Availability, etc.
Both plywood and engineered wood are versatile products that have numerous applications. Engineered wood is also likely to find its way in the manufacture of cabinetry, doors, and furniture, but plywood is more suited for tough applications like roofing, subflooring, and exterior construction.
One of the principal things to take into account is emissions. Most engineered wood products have formaldehyde-based adhesives which release unsafe gases over time. Low-emission products are available in both classes, however. Plywood itself can also release formaldehyde but is less objectionable from firms making it according to environmental standards.
Availability-wise, the two materials are available, although plywood is found in a larger variety of sizes and thickness, and hence, is more practical for bigger projects. Engineered wood, though, is normally manufactured in homogenous sheets and is easier to cut and mould, and is hence more convenient for complex patterns and precise furniture manufacturing.
Final Thoughts: Which One Should You Choose?
Finally, the decision is yours based on your particular project needs. For a cost-conscious project that will not need maximum durability, you might look at engineered wood products such as MDF or particle board. These provide uniform performance and convenience for interior use with smaller sizes.
If you require a material that can withstand heavy loads, is water-resistant, and will endure decades, then plywood is your material. It's stronger, more versatile, and can withstand tougher conditions, and thus best suited for high-stress applications.
Why Choose Plywood?
Plywood is a strong choice for anyone in need of strength and stability for their project. Plywood is the most robust choice with unmatched durability and is an ideal material for applications involving heavy usage such as flooring, construction, and furniture. Plywood also offers flexibility in its design with potential for several different creative purposes. Its composite layer design will resist warping and cracking while continuing to offer long-term performance.
Further, plywood is better suited for performance in the outdoors or wet environments than wooden material because it is resistant to water. Additionally, despite being more expensive, the strength and resilience you receive from using plywood are worth every penny for quality woodworking.

FAQs:
-
What is the main difference between engineered wood and plywood?
Ans. Engineered wood is made from wood fibers or particles bonded with adhesives, while plywood is made from layers of wood veneers glued together. The main difference lies in their composition and structure.
-
Which is more water-resistant: engineered wood or plywood?
Ans. Plywood is generally more water-resistant, especially types like marine plywood. Engineered wood, such as MDF, is more prone to moisture damage unless treated.
-
Is engineered wood cheaper than plywood?
Ans. Yes, engineered wood is generally cheaper than plywood, making it a more cost-effective option for many projects. However, this comes at the cost of some durability and strength.
-
Can I use engineered wood for furniture?
Ans. Engineered wood is suitable for indoor furniture, particularly for pieces that don’t endure heavy wear. It’s often used for cabinetry and shelving but may not be as durable as plywood for high-use furniture.
Which is more durable for long-term use?
Plywood is more durable for long-term use, especially in high-stress applications like flooring or outdoor furniture. It offers superior strength and resistance to warping over time.